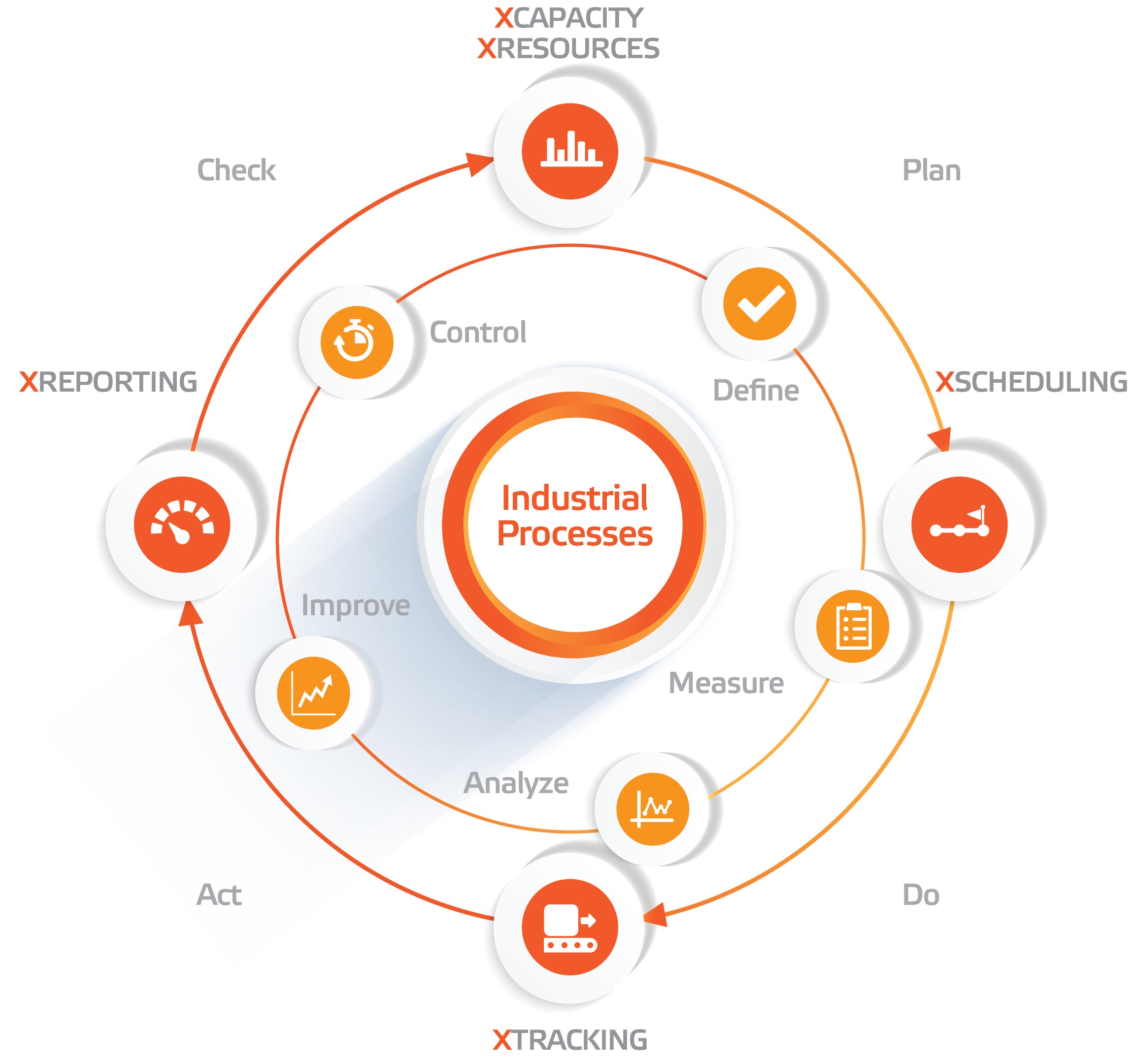
XMOM and Lean Six Sigma
XMOM(Manufacturing Operations Management) systems for managing production processes can be used as a tool for implementing Lean Six Sigma methodology. The link between the function of XMOM and the ideology of LSS creates the ideal environment for long-term growth and improvements through:
-
A system for production scheduling and re-scheduling in real time which optimizes the used material, reduces operational time and reduces stockpiles;
-
Tracking system which monitors live the movement of each product and the accompanying processes which helps to improve quality control and to reduce defect products;
-
Standardization and traceability of processes through constant flow of information which helps take short and long-term decisions to improve work effectiveness;
-
A system for generating reports and indices based on constant flow of information from production processes, which allows the isolation and elimination of processes that do not bring added value.
What is “Lean”?
The Lean methodology was first introduced by Henry Ford through his assembly line and later Taichi Ono created and applied Lean management philosophy and practices in the production of Toyota.
Lean in short is a systematic approach to identify and reduce losses (processes which do no not add value). The purpose of this methodology is to improve production operations by:
-
Eliminated processes that do not produce added value;
-
Reducing execution time and costs;
-
Increasing production capacity;
What is “Six Sigma”?
Six Sigma is a strategy for quality control which was introduced by the US company Motorola in 1981 and since then it has helped numerous organizations from various industries around the world to save huge amount of money.
Six Sigma is a statistical method based on the concept “variations of the process” that takes into account different variables (eg the waiting time for a product in front of a work center which can vary from seconds to minutes). The ultimate goal is to improve the production process so that the accumulated defects are no more than 3.4 in 1 million – production quality of 99.9997%. The results from implementing the Six Sigma strategy are increased turnover and greater customer satisfaction.
All Six Sigma projects are based on the DMAIC framework which has 5 phases: Define, Measure, Analyze, Improve and Control. Each of these phases contains a set of tools and techniques to help improve the production process from beginning to end.
Lean Six Sigma
In the 1980s consultants and professionals trained in both Lean and Six Sigma realized the synergy between them. They started combining different tools from Lean ( focused on reducing waste) and Six Sigma ( focused on improving quality). That is how the methodology Lean Six Sigma ( LSS) was created which aims to improve the strengths and minimize the weaknesses of both approaches.
LSS initially focuses on the use of the Lean methodology and tools to identify and remove the “waste” in order to reduce production time and then to identify and reduce variations in order to improve quality through Six Sigma.
Benefits of LSS:
-
It helps develop employees by involving them in different processes for continuous improvement;
-
Reduces costs by eliminating steps in manufacturing, which do not produce added value;
-
Increases revenue by simplifying processes and reducing production time;
-
Increases production capacity by permanently improving the processes involved in the production